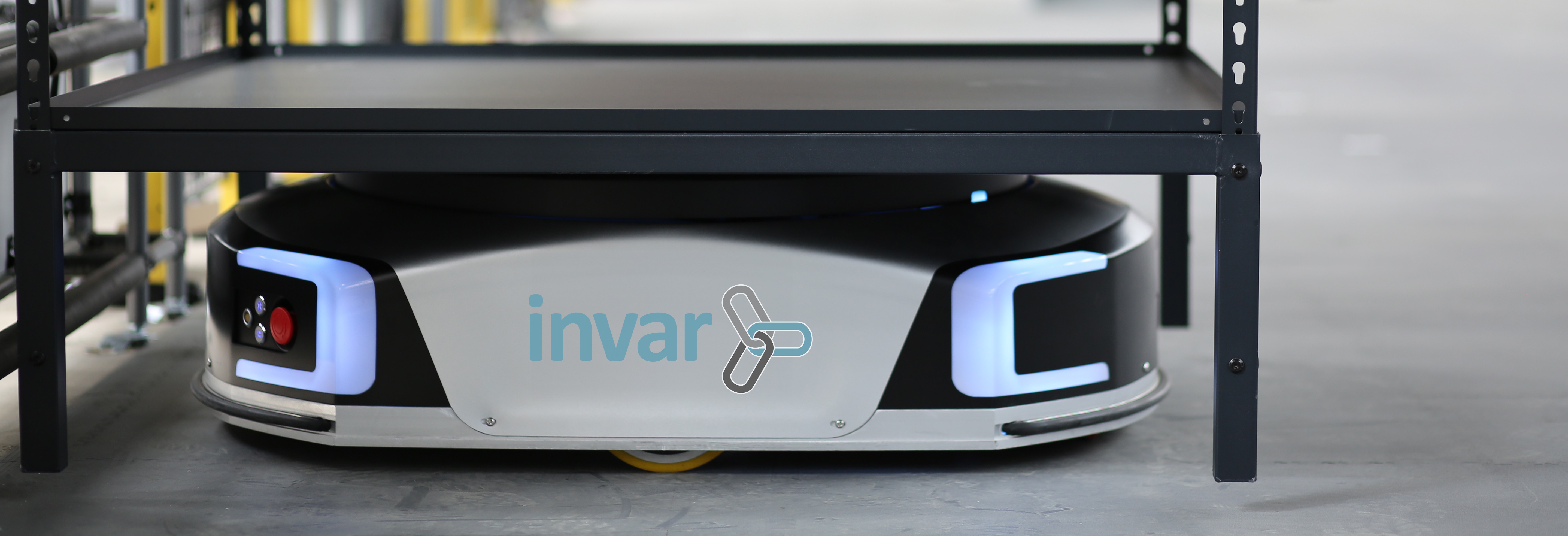
AMRs in the spotlight: Manufacturers (B-Tier)
Is the robotic revolution really right round the corner? Is automation the automatic assumption of our assured future? Are AMRs the axiomatically mature result of the next generation of intralogistics? When we answer that question, it might be helpful to think out of the box of what we talk about when we talk about this kind of equipment and its uses.
We very often find ourselves thinking about places such as “warehouses” or “storage facilities”, “distribution hubs” and “commercial outlets”. Less considered, but just as important is the matter of manufacturing. Factories. Assembly plants. Construction operations. All of these and more present use cases for intralogistical robotics of all kinds.
But do AMRs fit well into the niche here? That is what the Invar group intends to investigate.
With an overall careful consideration, and an examination of the logics behind logistics, it makes sense to put manufacturers into the B tier when it comes to AMR applicability.
Routing – Really? – One of the main advantages offered by AMRs is their ability to manage, calibrate, and co-ordinate complicated routing decisions around an operational area. When working in B2C ecommerce environments, AMRs can find the fastest connecting routes between where the novelty coffee mugs are kept, navigate from there to the spritzing spray bottles, before finally locating the aquamarine dress shirts, and then heading over to the packing areas. Organising routes this varied, alongside all the other robots with equally complex pathing to process, is an elaborate task, and a huge boon for many different sectors ideally placed to make use of AMRs.
However, when it comes to manufacturing, this is not a major concern. In many, arguably most, cases, manufacturers are making a single, or a small subset of items in their facilities. The AMRs need to simply repeat the same course down an assembly additive processing line over and over again. This task can be accomplished perfectly well by AMRs, but a conveyor or automated forklift system could do the very same thing just as well. With that realisation, the question becomes why exactly you’d want something so advanced to perform a task so relatively simple.
However, there are answers to this:
The Space solution – One of the major advantages AMRs offer to every sector is space consolidation. To perform all the radically complicated navigation and mobilisation of goods, AMRs need a radically lower space profile than many of the other available alternatives. Static ASRS (automated storage and retrieval systems) require huge volumes of space to be consumed by racks, rails, tracks, and any number of other such apparatus and ephemera. By contrast, AMRs contain all their movement and navigation technology inside themselves, with only a few subtly placed sensor reflectors and data matrix codes affixed to the floor.
In the manufacturing world, the huge advantage of space saving is that more space can be allocated to the assembly equipment. By minimising the space needed to move the goods, and maximising the availability of space for technological edges, you make much more of the business's assets oriented directly around the company’s necessary imperative. The construction of goods for sale. The more space you have for making means you can make more things in better ways. All the better for the manufacturing mindset.
Flexibility – Perhaps the single biggest specific advantage of AMRs for the manufacturing space is their flexibility. Unlike fixed conveyor belt systems or a static ASRS operation, AMRs can be rerouted and reprogrammed to take different directions as and when needed. While this may not be required most of the time, there is a specific kind of crucial moment for manufacturers when such flexibility will be extremely valuable. Any occasion where equipment, methods, processes, or other patterns need changing.
With AMRs you have none of the obstructive and difficult infrastructure of apparatus that comes with an ASRS or any of the other options. If you need different equipment, or your factory needs to expand, contract, or otherwise change, robots can be moved away, reprogrammed, and redeployed into a new pattern as and when required. The alternative options in this area would take a gargantuan volume of work to finish and fix up. The expense and effort would doubtless be disruptive and would ultimately result in potentially costly delays. The flexibility of AMRS is a huge boon to the manufacturing sector specifically. A good reason to seriously consider them as part of any automation options in your future.
Carrying capacity – However while AMRs might save space in some ways, the counterpoint is that there is a very good reason that conveyors and static ASRS take up such large volumes of space. It isn’t because they’ve been over-doing it on the nuts-and-bolts diet. Rather, the space consumption is directly proportional to the power and weight capacity offered by these systems.
AMRs in their current form simply cannot carry the same levels of weight and volume that conveyors and static built ASRS can handle. The upper limits of a few tons emerge as a natural result of AMRs needing to contain all their motorization and mobility equipment in the small low profile frame offered as part of the AMR overall package. By contrast, powerful engines and extensive power reserves and distributors can be layered into the more robust and powerful infrastructure of a static built ASRS.
This then moves the question of AMR applicability onto “what are you manufacturing”. If you are making smaller scale items, products that weigh a tonne or less, then AMRs could well suit your needs. Bulkier items and heavy industrial processes, however, would not do well with this technology at this stage. Which is not to say robots are off the table. It may well be a case for automated forklifting equipment. But for now, AMRs are not part of the heavy industrial future.
Talk to Invar about your options – Maybe you think that robotic forklift trucks might be the backbone of your future business plans. Or maybe you are more encouraged by the thought of an ASRS with inbuilt racking and rails. Or perhaps you are imagining that with the right conditions, AMRs might make your manufacturing plans work really well. If you want a wider perspective on the issue, talk to Invar today.
Written by

Michael Trimmer

Contact Us
Contact us for further independent advice on transforming operational performance in the warehouse.
Contact usRelated Articles

AMRs in the spotlight: Wholesalers
Autonomous mobile robots, or AMRs, are very often imagined to be a very specific kind of future...
Read More
AMRs in the spotlight: Pharmaceuticals
What do Issac Azimov, Hollywood blockbusters, and the wider intralogistics community have in...
Read More
AMRs in the spotlight: B2C Ecommerce
If you think of “New technologies” and “Intralogistics” the letters “AMR” often naturally follow....
Read More